From iron waste to mushrooms, the world of concrete alternatives is exploding with innovation. Here's what's out there now, and what's to come.
7 Concrete Alternatives
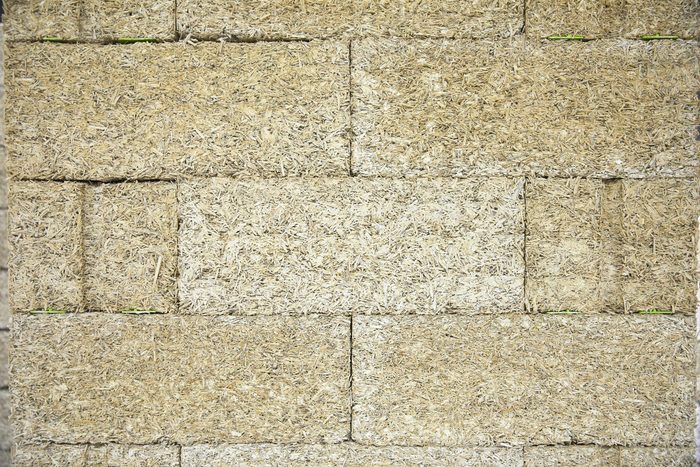
Hempcrete
Hempcrete is made from the woody cores of hemp plants (aka hemp hurd), mixed with lime, sand and water. The resulting product is one-eighth the weight of concrete and resistant to mold, insects, fire and earthquakes. It can’t be used as a foundation or in load-bearing walls, but works for interior walls.
It comes in prefab panels, bricks, cinder blocks and insulation. Its insulation R-value runs between 2.4 and 4.8, compared with fiberglass batts at 2.2 to 4.3. It’s also an environmentally friendly replacement for drywall.
Hempcrete is ultimately a carbon-negative product, because the plants sequester CO2 while they’re growing, and the products sequester CO2 once they’re installed in buildings. Hempcrete production also uses much less water than concrete production. Prices vary widely depending on local availability, but are typically more expensive than standard concrete.
Compressed Earth Blocks
Several variations of compressed or rammed earth blocks can be found on the market.
While similar to adobe and other centuries-old processes, modern earth blocks often have fibers, bamboo or rebar in them for added strength. They’re also fire-resistant, with great insulating properties. Higher-performing earthen blocks can be used in lieu of any standard masonry products.
Environmentally, they’re a climate-conscious choice because they’re unfired, don’t have lime and are often made locally from already mined materials, like overburden (i.e. the extra soils above quarries that would otherwise be discarded). Cost ranges widely, but can be as cheap or cheaper than concrete.
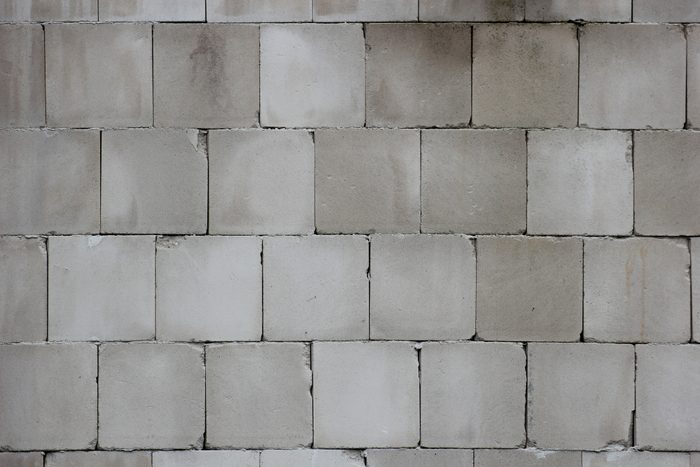
Green Concretes
In several hybrid concretes on the market, like ashcrete and fiber cement, more eco-friendly materials replaced some of the energy-intensive ones.
Ashcrete uses fly ash from coal combustion. This strategy hearkens back at least as far as the Romans, who used volcanic ash to build aqueducts and other long-lasting buildings. In some cases, ashcrete is stronger than standard cement and cures more quickly.
Ashcrete can be a general substitute for Portland cement for everything from masonry blocks to columns and road construction. It’s often less expensive than standard concrete.
Fiber cement uses wood pulp, which is lower maintenance in coastal climates because it resists cracking and warping. Typically used as roofing and siding panels, it’s a little more expensive than vinyl siding.
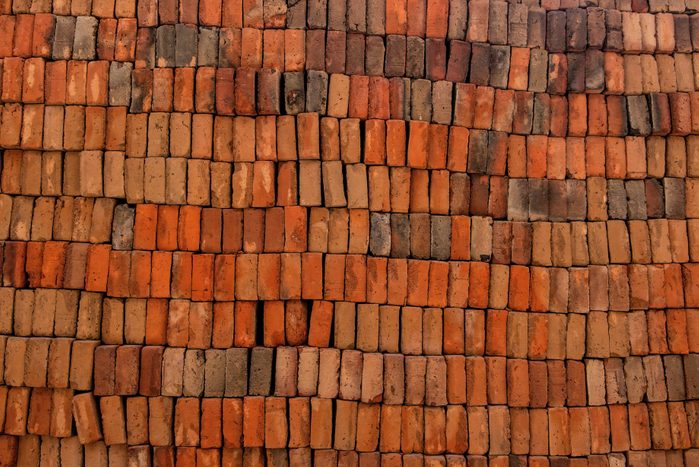
Ferrock
Ferrock uses 95% recycled materials, combining industrial steel dust waste and silica from ground-up glass. Those are mixed with water and exposed to high concentrations of CO2. The result: A carbon-negative concrete alternative up to five times stronger than regular concrete.
It also has better compressive strength and flexibility, which makes it good for earthquake-prone regions. Ferrock can be used as slabs and bricks in load-bearing situations, as well as for pavers and walkways. Because it’s relatively inert, it’s also fine for marine-based projects.
Environmentally, Ferrock is carbon negative because it absorbs more CO2 from the air than it releases in production. While not super expensive for small-scale projects, it’s not yet widely available for consumer purchase. Check with local contractors to see if they can get their hands on some for you.
Mycelium
Mycelium structures, aka mushroom block, are grown from fungi fibers. They’re one of a growing number of biomass building materials in development and on the market.
Mycelium is a lightweight, versatile material that can be grown into any shape. It’s fire, water and mold resistant, plus self-healing. It’s not easy to find in large quantities on store shelves, and costs vary widely. But you can actually grow your own mycelium for walkways, driveways and bricks.
Biomass ingredients like fungi and bacteria are also used as binders in more traditional cements. “They are providing a cemented product that you can mix with sand or rocks, but using natural processes like we see in coral reefs and so forth,” says Hubler.
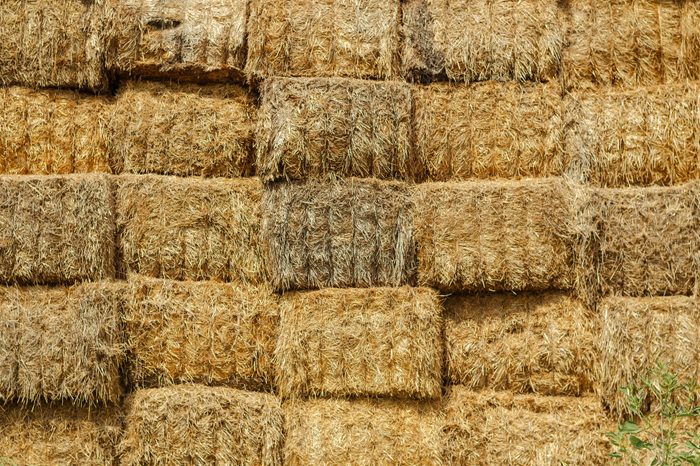
Straw Bales
This millennia-old building material got a reboot in the 1970s. Straw bale construction is essentially stacks of tightly baled straw, anchored with rebar, bamboo or wood, then covered with plaster or plywood.
Straw-bale walls are effective temperature and sound insulators, with up to three times the fire resistance of traditional homes. They’re also good for earthquake and wind resistance, but often not ideal for humid climates.
Straw is a renewable, nontoxic, carbon-friendly material that’s also affordable. While straw-bale construction is not embraced everywhere, some building codes do recognize it, and some local banks offer financing for straw-bale-home construction loans.
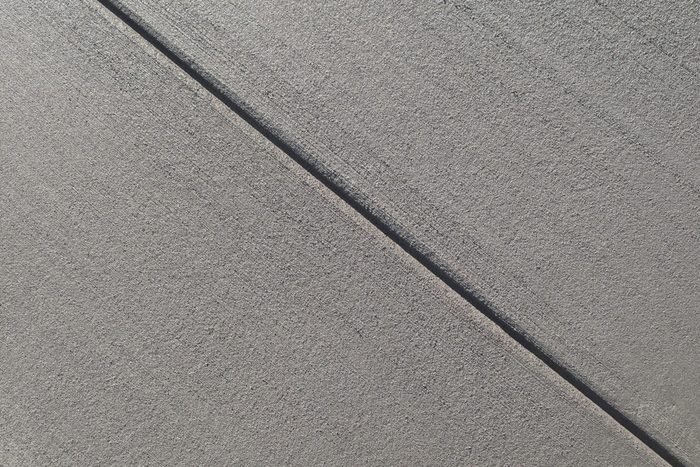
Regular Concrete
While concrete alternatives are the greenest choices, the concrete industry hasn’t been sitting on the sidelines. Hubler says they’ve been under a lot of pressure lately to revamp their traditional products.
“The concrete you buy right now already includes waste products to reduce the amount of cement it needs,” she says. “The ordinary Portland cement you get off the shelf is no longer just cement. It has a lower impact on the environment already because the whole industry is reimagining.”
Beyond ingredient shifts, other additives are being introduced into regular concrete as well.
“You may have noticed sometimes a crack in the sidewalk looks a little fuzzy,” says Hubler. “That’s because in some areas we’ve started putting polymer fibers in them. Pretty soon those fibers will be replaced with something that’s solid carbon, to sequester carbon into those products.”